Exploring the Globe of Steel Stamping: From Layout to Production
Within the realm of production, steel stamping attracts attention as a precise and reliable method for shaping steel sheets into various types with remarkable uniformity. From the first design phase where intricate patterns take form to the detailed manufacturing procedures, steel stamping is a mix of creativity and engineering. Looking into this world unveils an intricate interaction of creative thinking and technological proficiency, providing a glance right into a world where innovation satisfies craftsmanship.
Background of Metal Stamping
Steel marking, a widely made use of manufacturing procedure today, has a rich history that goes back to old times (Metal Stamping). The origins of steel marking can be mapped to old people such as the Egyptians, who utilized stamping strategies to decorate fashion jewelry and ornaments with complex layouts. With time, metal marking developed, with worlds like the Greeks and Romans using it for developing coins and decorative products
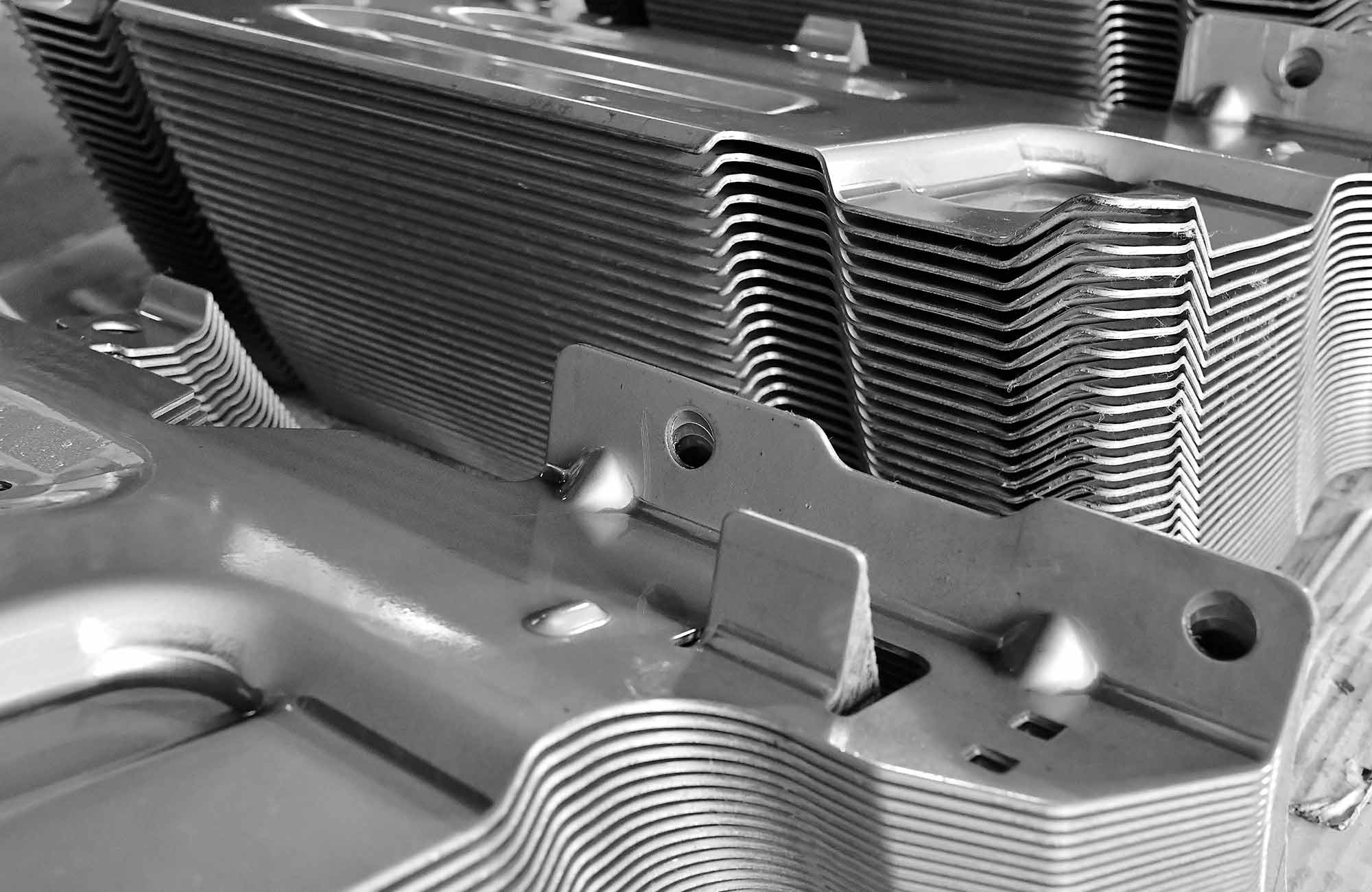
In the 20th century, metal marking remained to evolve with the assimilation of automation and computer system numerical control (CNC) innovation. These developments additionally enhanced the efficiency and precision of metal stamping processes, making it a vital component of modern manufacturing throughout industries such as automobile, aerospace, and electronic devices. Today, metal marking stays an essential manufacturing process, combining tradition with technology to fulfill the demands of a regularly advancing market.
Layout Factors To Consider and Prototyping
When establishing metal stamping projects, meticulous focus to create factors to consider and prototyping is necessary for ensuring optimum production outcomes. Design factors to consider in metal stamping consist of material option, part geometry, tooling layout, and manufacturing expediency. Selecting the right product is vital as it affects the part's performance, cost, and manufacturability. Component geometry influences the complexity of the marking procedure and the functionality of the final product. Tooling style plays a substantial duty in the success of metal stamping projects, affecting part precision, device durability, and manufacturing performance.
Prototyping is an important phase in the metal stamping procedure that enables engineers to examine the design, verify manufacturability, and make essential changes before full-scale manufacturing. By carefully taking into consideration design facets and utilizing prototyping, manufacturers can enhance the metal stamping procedure and achieve premium, affordable manufacturing outcomes.
Tooling and Equipment Fundamentals
Thinking about the essential role that tooling style plays in the success of metal stamping projects, recognizing the crucial tools and devices called for is paramount for achieving efficient manufacturing results. Tooling is a fundamental element of steel stamping, as it directly impacts the high quality and consistency of the end products. Vital tools consist of passes away, strikes, and components, which are custom-designed to form and create the steel into the desired components. Passes away are the key tool used to reduce and create the metal, while strikes aid create openings or details shapes. Fixtures hold the metal in location during the stamping process, guaranteeing precision and repeatability. Additionally, tools such as marking presses, feeders, and coil handling systems are essential for automating the marking procedure and enhancing efficiency. Purchasing top quality tooling and tools not just improves manufacturing efficiency yet also causes greater precision, reduced waste, and general price savings in steel navigate here marking operations.
Production Process and Quality Assurance
Efficiently taking care of the production process and executing robust quality assurance steps are necessary for ensuring the success of steel stamping projects. The production procedure in metal marking involves a collection of steps that must be meticulously collaborated to achieve optimal results. It starts with the prep work of raw products, followed by the setup of the marking equipment and tooling. Operators then feed the products into the press, where the marking operation takes place. Throughout this procedure, it is critical to check the production line for any type of issues that may influence the high quality of the stamped parts.
Quality control in metal stamping is extremely important to supply items that satisfy the required specifications. By keeping strict top quality control criteria, suppliers can copyright their reputation for providing high-grade steel marked products.
Applications and Industry Insights
In the world of metal marking, the effective application of manufacturing procedures and top quality control actions straight affects the effectiveness and dependability of various industry applications and gives important insights into check these guys out the field's functional dynamics. Metal marking discovers prevalent application across diverse industries, consisting of vehicle, aerospace, electronic devices, and devices. In the vehicle sector, steel marking plays an important role in Home Page producing elements such as chassis, braces, and structural parts with high accuracy and effectiveness. The aerospace industry depends on steel marking for producing complex parts like panels, braces, and fittings that fulfill stringent quality standards (Metal Stamping). In the electronics market, metal marking is utilized to create exact parts like connectors, terminals, and heat sinks. Additionally, steel stamping promotes the manufacturing of various family devices, including fridges, washing devices, and ovens, by supplying economical options for producing resilient and intricate components. Comprehending the applications and market insights of metal stamping is essential for optimizing manufacturing processes and improving item quality throughout different markets.
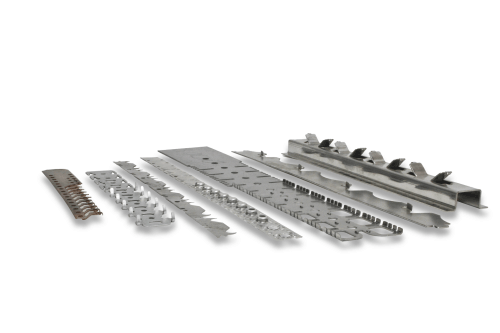
Conclusion
Style factors to consider, prototyping, tooling, equipment, production processes, and quality control are important elements of steel stamping. With its prevalent applications and market understandings, steel stamping continues to be a functional and reliable manufacturing procedure.